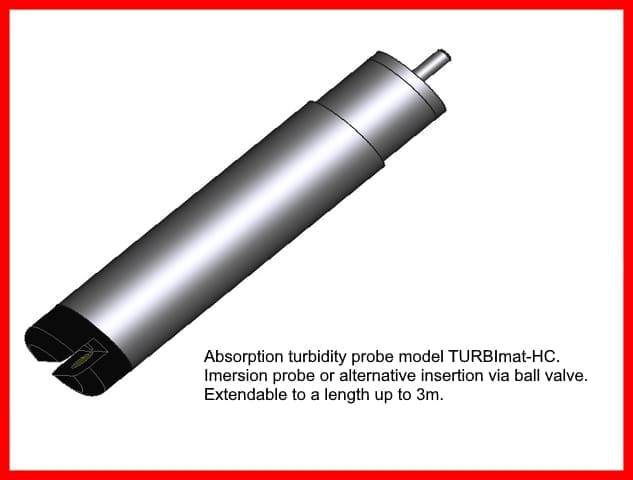
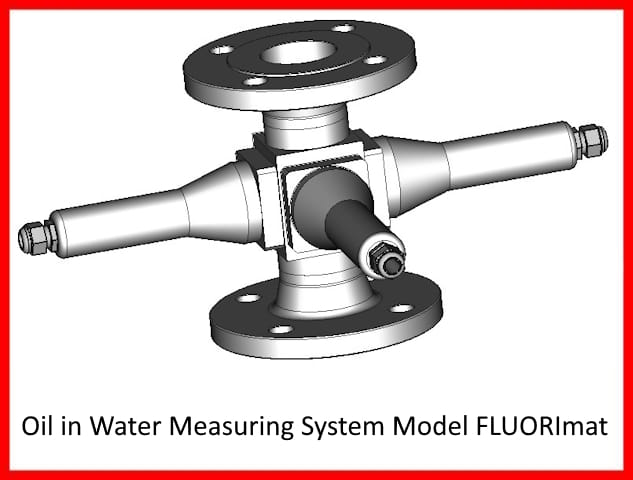
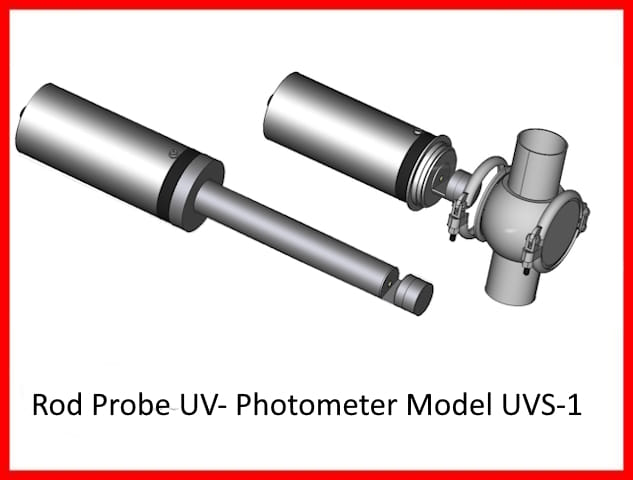
Sensor- / Probe materials inline Photometry
Material Characteristics of the Wetted Parts of Flow Cells and measuring Probes.
The Chemtronic / Monitek sensors will be produced in various materials depending on the requirements of customer’s application. This page contains a list of the most common materials and their characteristics used for the wetted parts of our process turbidimeter and photometer.
Stainless Steel
Hastelloy
Titanium
Monel
PVDF (Kynar)
VICTREX® PEEK™
Stainless Steel
Stainless Steel is the current term for a rustproof and acid resistant steel.
It is an alloy of iron with a minimum of 10,5 to 13% chromium. The chrome causes an austenitic or ferritic mix-cristal structure. The corrosion resistancy is based on the fact, that the high chrome content causes a sealed passive layer of crome oxyde at the steel surface. Other alloy materials like nickel, molybdenum, manganese and niobium optimize the resitance against corrosion and cause a better mechanicle characteristics. Typically a high chrome content combined with a lower nickel content is prefered to receive a good corrosion resistance, because chrome is cheaper than nickel.
Corrosion:
Stainless Steel can get extreme corrosion under conditions like the environment of indoor pools with a high clorine content in the atmosphere, or in offshore applications. It is very important to select the correct material to get a good corrosion resistance against products and enviroments with a high content of chloride ions. To receive a good resistance against the cloride ions typically 2% Molybdenum is added to the alloy (example: X2CrNiMnMoNbN25-18-5-4). Other Stainless Steels like X5CrNi18-8 do not show any resistance against specific acids like hydrochloric acid (34 % HCl). The metal becomes solved totaly over time. The use of Stainless Steel became more and more common since the patent „Steel with high resistance against corrosion“ was given to the German company Friedrich Krupp AG in year 1912.
Chemicle and Mechanicle Characteristics:
Although Stainless Steel can be machined rather bad, the use of Stainless Steel offers mostly advantages like long lifetime, good hygiene, low cost as well as environmental advantages during production. Other advantages are easy weldability and low magnetism. The disadvantages are the lower tensile strength , the missing hardenability compared to other steel and the worse antibacterial effect compaired to copper and copper alloys (oligodynamic effect). Hardenable martensitic-ferritic stainless steel alloys are available to produce tools like shears or knifes. They often contain vanadium and molybdenum; typical examples are X30Cr13 and the high- quality alloy X50CrMoV15. Ferritic- austenitic Duplex steel like X2CrNiMoN22-5-3 is used for offshore applications. Cheap manganese can be used for austenitic steel as well instead of nickel , but the total quality of this alloys are typically lower.
Special materials like X2CrNiMoN17-13-5 (material no.: 1.4439/Alloy 317 LN) are prefered to fit the requirements of offshore applications. Screw materials and their describtion are standardized in EN ISO 3506. The European standard DIN EN 10088, Part 1-3 specifies the general technical conditions to meet the requirements of not corrosive steels. The PRE- value specified in this standard is used to get information regarding the corrosion resistance of steel, as higher this number as better the resistance against corrosion. Alloys with a PRE-Number above 33 are sea water resistant. International Organization for Standardization: ISO homepage
Deutsches Institut für Normung E. V.: DIN homepage
Intergranular Corrosion:
The resistance against corrosion becomes lower with a growing carbon content. Chromium has a high carbon affinity. Carbon causes the formation of hard and inflexible chromium carbide instead of the protecting chrome oxyde layer. Therefore a high content of carbon will cause the tendency of intergranular corrosion. The content of carbon should be as low as possible to work against this effect and to raise the weldability of Stainless Steel. The appropriate steel grades can be stabelized with niobium or titanium because these metals show a higher affinity to carbon as the chromium.
Overview of the material designations
Material Characteristics of the Wetted Parts of Flow Cells and measuring Probes.
This table shows the general rustproof and acid resistant steels.
DIN ENMaterial no. | DIN ENShort designation | ASTM/AISIDesignation | UNSDesignation |
1.4016 | X6Cr17 | 430 | |
1.4512 | X2CrTi12 (alt X6 CrTi 12) | 409 | |
1.4310 | X10CrNi18-8 (alt X12 CrNi17 7) | 301 | |
1.4318 | X2CrNiN18-7 | 301LN | |
1.4307 | X2CrNi18-9 | 304L | S30403 |
1.4306 | X2CrNi19-11 | 304L | S30403 |
1.4311 | X2CrNiN18-10 | 304LN | S30453 |
1.4301 | X5CrNi18-10 | 304 | S30400 |
1.4948 | X6CrNi18-11 | 304H | S30409 |
1.4303 | X4CrNi18-12 (alt X5 CrNi18 12) | 305 | S30500 |
1.4541 | X6CrNiTi18-10 | 321 | S32100 |
1.4878 | X10CrNiTi18-10 (alt X12 CrNiTi18 9) | 321H | S32109 |
1.4404 | X2CrNiMo17-12-2 | 316L | S31603 |
1.4401 | X5CrNiMo17-12-2 | 316 | S31600 |
1.4406 | X2CrNiMoN17-11-2 | 316LN | S31653 |
1.4432 | X2CrNiMo17-12-3 | 316L | S31603 |
1.4435 | X2CrNiMo18-14-3 | 316L | S31603 |
1.4436 | X3CrNiMo17-13-3 | 316 | S31600 |
1.4571 | X6CrNiMoTi17-12-2 | 316Ti | S31635 |
1.4429 | X2CrNiMoN17-13-3 | 316LN | S31653 |
1.4438 | X2CrNiMo18-15-4 | 317L | S31703 |
1.4539 | X1NiCrMoCu25-20-5 | 904L | N08904 |
1.4547 | X1CrNiMoCuN20-18-7 | S3 |
Hastelloy
HASTELLOY® Alloy C-22 -is a versatile applicable material for use in chemical industry and offshore. HASTELLOY is a registered trade name of the Cabot corporation, Boston, MA The HASTELLOY®-alloy C-22 is made from a critical composition of the alloying elements chrome, molybdenum and tungsten.
The relationship of these alloying materials causes an optimal corrosion resistance in the Ni-CRMo-system against oxidizing and not-oxidizing acids as well as against hole and intergranular corrosion. Beyond that Alloy C-22 has an excellent thermal stability and allows welding methods with high heat. HASTELLOY alloy C-22 material solves difficult problems with corrosions in practice, where other alloys of highcorrosion resistant materials fail. The alloy is used for the construction of pressure vessels with temperature ranges between -196°C and 400°C.
Hastelloy alloy C-22 is comparable in its mechanical behavior to the other alloys of the C-type. The material has a high tenacity at low temperatures, even under cold-transformed conditions. It is well weldable.
Titanium
Titanium is a chemical element in the periodic system of the elements with the symbol Ti and the ordinal number 22. It belongs to the transition metals, light, strong, flexible, white-metallically shining and corrosion resistant. It is suitable for applications, which require a high corrosion resistance, strength and a low weight.
History
Titanium was discovered 1791 in England by the clergyman and amateur chemist William Gregor in the titanium iron. The element has been re- discovered 1795 by the German chemist Heinrich Klaproth. In the rutile ore, he named the new element titanium. Pure titanium metal (99.9%) was manufactured for the first time 1910 by Matthew A. Hunter. He heated titanium tetrachloride with sodium to a temerature of 700°C to 800°C and received the pure element. The developement of the industrially accomplished reduction of titanium tetrachloride with magnesium (Kroll process by William Justin Kroll 1946) opened the use of titanium for commercial applications.
Properties
Titanium produces in contact with air an extremely steady oxidic protection layer, which makes it corrosion resistant in many products. A remarkable charateristic of Titanium is the extreme strength and the low density of the material. This properties will decrease very fast at temperatures above 400°C. Ultrapure Titanium is ductile. At higher temperatures it embrittles very fast due to the taking of oxygen, nitrogen and hydrogen. To consider is also the high reactivity of titanium with many products. The speed of reaction can cause an explosin at increased temperatures or increased pressure, if the passive layer is not strong enough to defend the chemical attack.
Material Characteristics of the Wetted Parts of Flow Cells and measuring Probes.
Titanium burnes in pure oxygene at a temperature of 25 °C and a pressure of 25 bar to pure titanium oxyde. It reacts automatically with oxygene at temperatures above 880°C, at temperatures above 550°C and reacts („burnes“) as well in pure nitrogene. These characteristic must be absolutely considered at heat developing processes like the machining of titanium.
Titanium is stable in diluted hydrochloric acid, chloride containing solutions and most organic acids. The operating conditions are to be kept strictly, due to the danger of an explosion at applications with chlorine gas.
Monel
Monel, as well known as Monel metal, designated after Ambrose Monel († 1921), is a nickel-copper-alloy (approximately: 65% nickel, 33% copper and 2% iron) with high tensile strength, which behaves very steadily in relation to atmospheric corrosion, sea water, multiple acids and alkaline solutions. The designation Monel is a protected label name of the company Special Metals corporation, Huntington (West Virginia), USA. The material is considered as a forerunner of the stainless steel.
Material Characteristics of the Wetted Parts of Flow Cells and measuring Probes.
Monel is used in the naval- and offshore technology , for example turbine construction, equipment in chemical and hydrocarbon industry, as material for valves, pumps and heat-transfer sytems. It is remarkably stable against the aggressive Fluor F2 (passivation of the Monel surface by fluoridation) and is therefore used as material for F2- storage vessels (pressure bottles).
TFM™ PTFE
TFM™ PTFE is a branched polymer, with the formula: —[(CF2)4– CF(-O-CF2-CF2-CF3) — (CF2)5]n— The by-fluoridated side group is identically to the side group of PFA, but TFM™ PTFE contains clearly smaller quantities of these group. The molecular weight of TFM™ PTFE is 80% less in weight than that of PTFE. The molecular weight of PFA is 99% less in weight compaired with PTFE. Therefore it fills the characteristic gap between PTFE and PFA without disadvantage that it has to be processed by the injection molding method.
Characteristics:
TFM™ PTFE is temperature steady from -200°C up to +250°C in continuous operation. TFM™ PTFE is absolutely chemical resistant and therefore univeral applicable. The permeation rate of gases by TFM™ PTFE is clearly smaller compaired with PTFE and only insignificantly higher compaired with PFA. The surface finish of TFM™ PTFE is clearly improved compaired to PTFE. TFM™PTFE is weldable the material by using special methods, a consequence „of the shift towards thermoplastic “. TFM™PTFE has an improved cold flow, voids content and a better „Stretch Void“ index..
Other:
TFM™PTFE can be mixed with organic materials such as glass fiber, graphite or carbon. These compounds improve the material characteristics substantially, above all the pressure strength, thermal expansion, electrical values and the abrasion. The electrical resistance of the material wil be reduced by using carbon as additive. Therefore there is no danger of static discharge in case of using a TFM™ PTFE +25%C compound in hazardous area.
PVDF
The introduction on the market of PVDF (polyvinylidene fluoride) was 1961 by Pennwalt Corporation under the label name „Kynar “.
The piezoelectric effect of PVDF has been discovered by Kawai. Because of its good thermal and chemical stability PVDF is used as coating material for pipes or external construction components. It is as well used for seals, diaphragms and packing foils. Further PVDF finds its application in the measuring technique, e.g. for the coating of measuring probes.Since the material shows a strong piezoelectric effect, it is used also in microphones, hydrophones, loudspeakers and actuators.
UV- and gamma radiation
PVDF has a good stability against UV- and gamma radiation, therefore PVDF shows an extreme high resistance against ageing.
Physiological safety
PVDF is suitable in accordance with FDA „Title 21, Code of Regulations (USA) Chapter 1, part 177.2510“ for the safe use of articles, which are intended for repeated contact with food. Kynar is certified for the use in processing installations and storage devices „US-Department of Agriculture (USDA)“. PVDF corresponds also to the criteria of the „3-A Sanitary Standards for Multiple-Use Plastic Materials. Used as Product Contact Surfaces for Dairy Equipment, Serial-No.2000“.
Growing of micro organisms on PVDF
The surface of PVDF has the same unfavorable condidion for the growing of micro organisms as glass, this is the final result of an examination ordered by Solvay and proceeded by „Centre d‘ Enseignement et de Recherches des Industries Alimentaires et Chimiques“ (CERIA in Brussels). Due to these characteristics PVDF is used in the food industry (e.g. in dairies) as well as in pharmaceutical industry (e.g. for sterilizable high precision dosing pipettes) and in the clean rooms of the semiconductor industry.
Chemical resistance
PVDF has an extreme chemical resistance against the most inorganic and organic acids, oxidizing products, aliphatic and aromatic hydrocarbons, alcohols and halogen containing solvents. It resists halogens – specially bromine (but not fluorine) – and weak caustic solutions. It will be decomposed by fuming sulfuric acid, some strong basic amines, concentrated and hot alkalis as well as by alkali metals. In strongly polar solvents, like acetone and ethyl acetate, it pours and is somewhat soluble in solvents like Dimethylformamide and Dimethylsulfoxid.
VICTREX® PEEK™
First-class performance thermoplastic with remarkable characteristics.
VICTREX PEEK polymer is an aromatic, part-crystalline thermoplastic from the group of the Polyaryletherketone (PAEK). It can be processed with all usual thermoplastic procedures and is defined by a combination of excellent characteristics: excellent chemical resistance, excellent tribologic-, thermal-, electrical- and mechanical characteristics as well as dimensional stability.
PEEK has:
- a permanet operating temperature of +250°C, briefly to +300°C
- excellent mechanical characteristics
- excellent chemical and radiation resistance
- resistance to hydrolysis
- no out gassing in the vacuum
- very good tribologic characteristic
Machined parts from PEEK keep their unusually good mechanical characteristics over a long time and at very high temperatures.